Catch battery defects in hours–not weeks.
Detect issues and diagnose root cause faster, with data you already collect. Significantly reduce manufacturing ramp-up time with Voltaiq battery quality analytics.
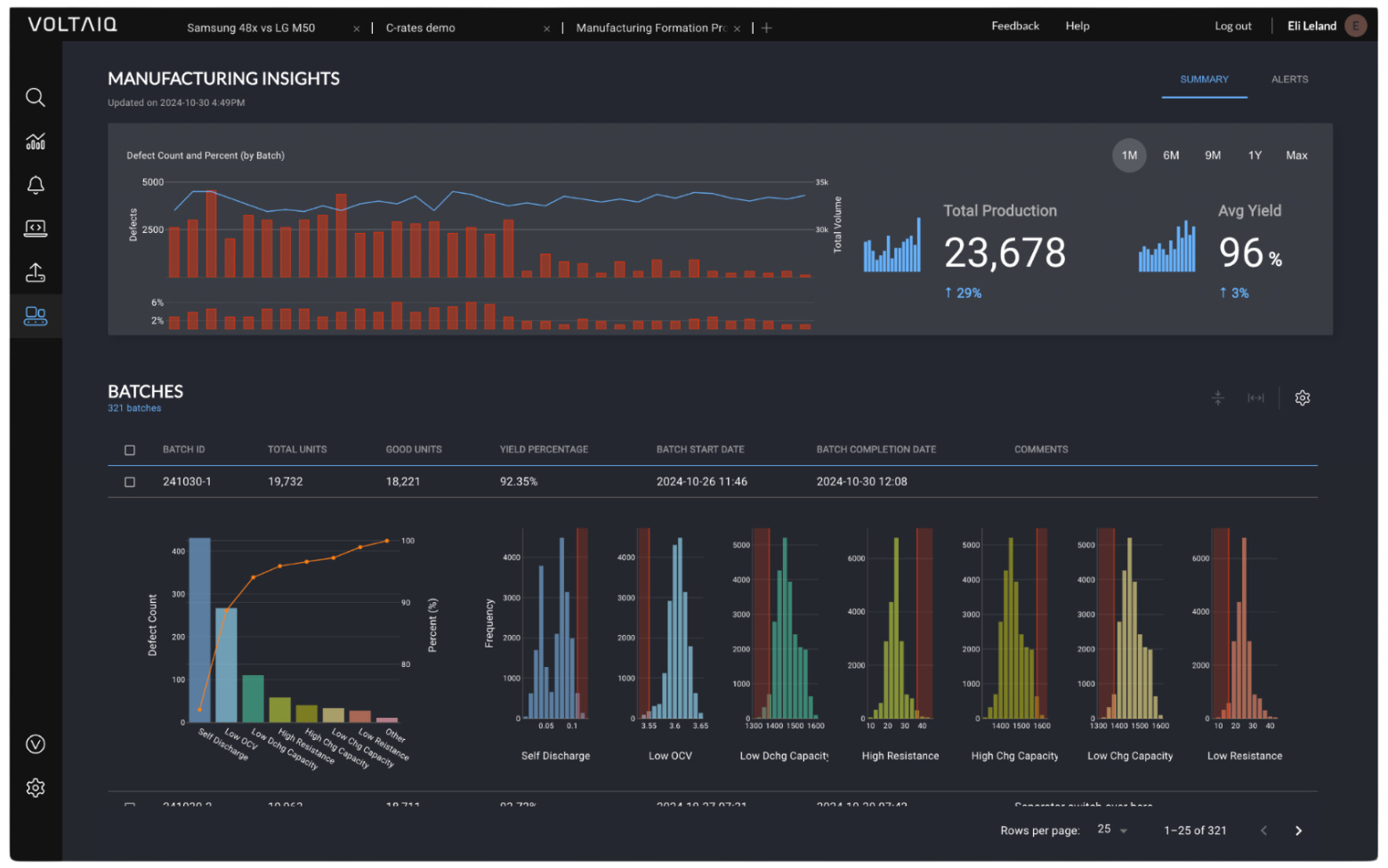
Trusted by leading battery manufacturers and OEMs.
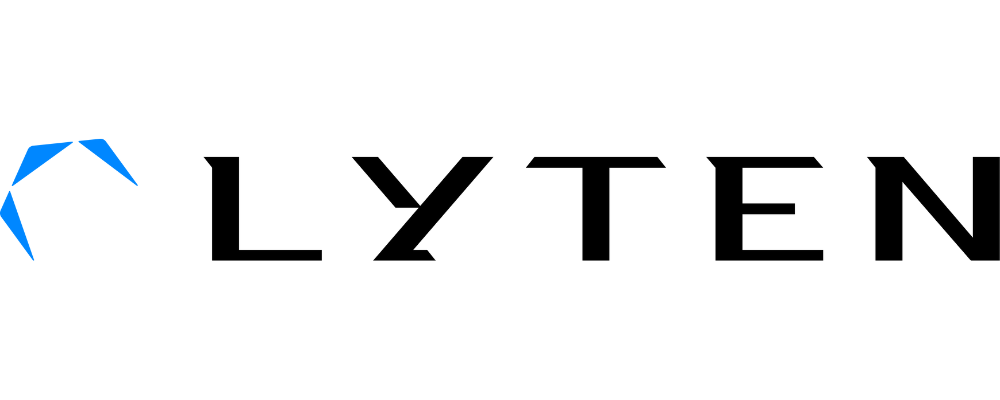
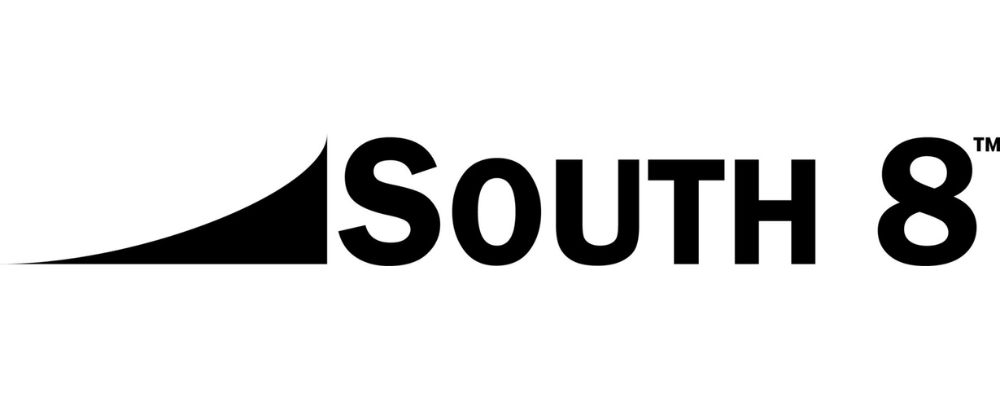
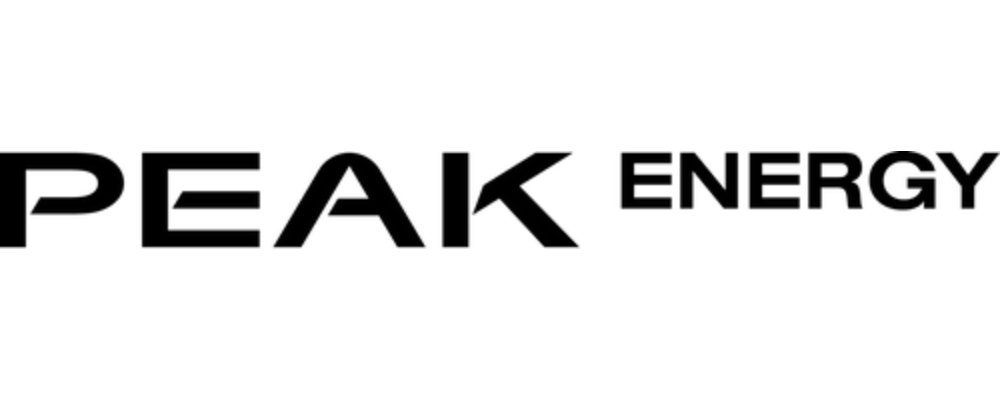
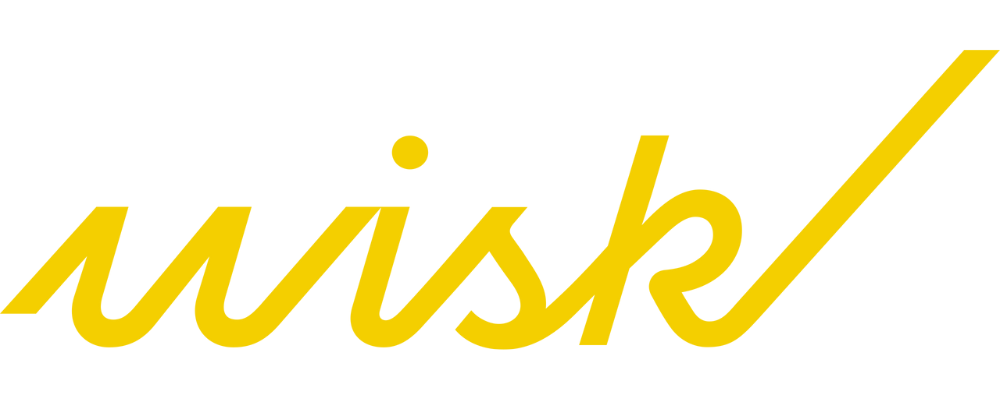
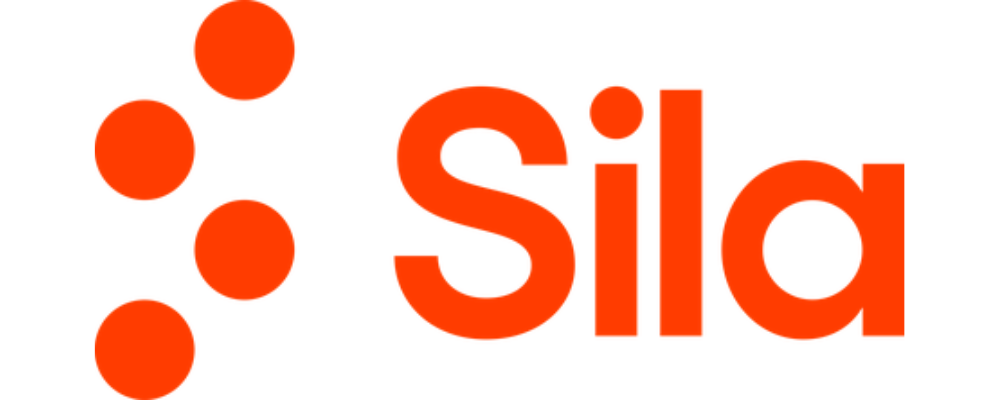
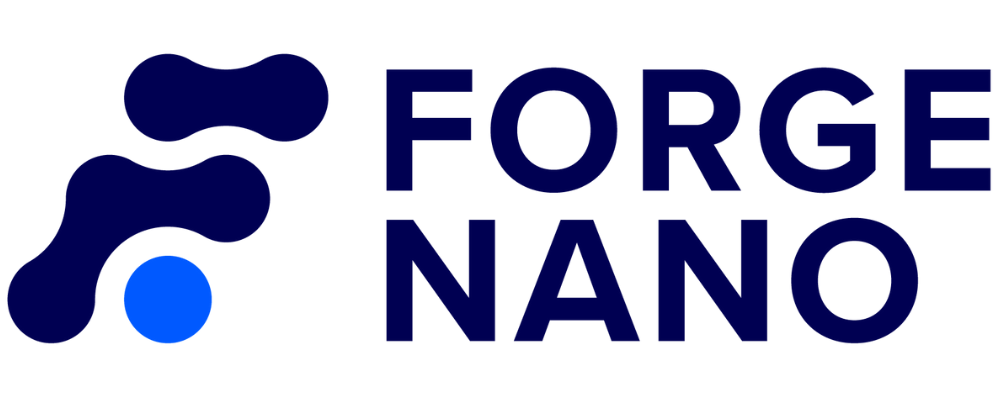
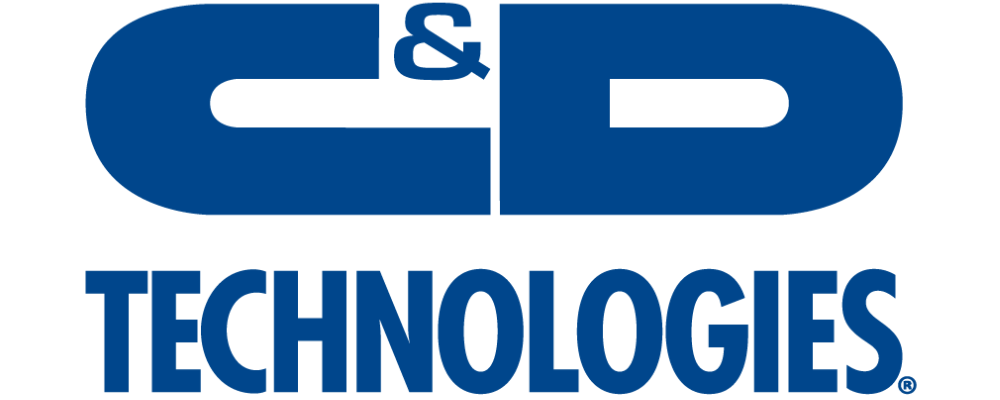
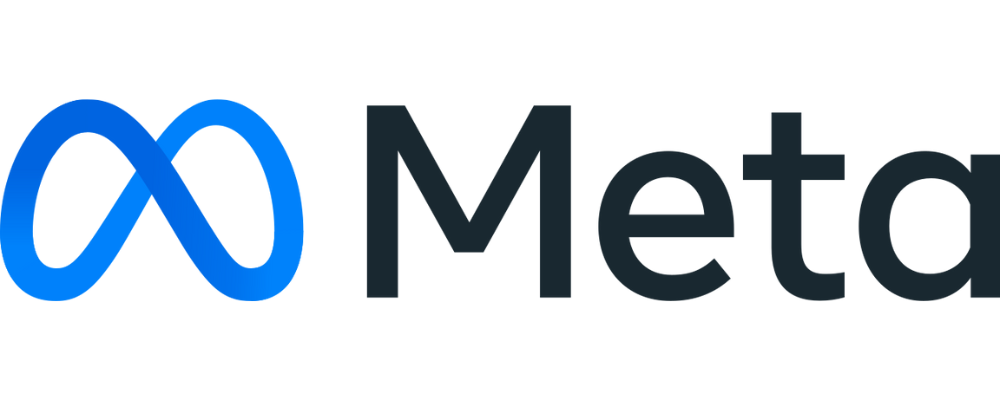
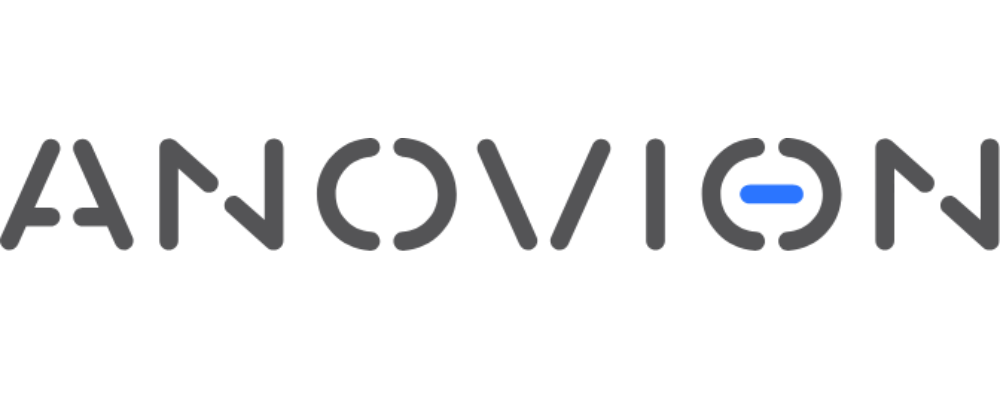
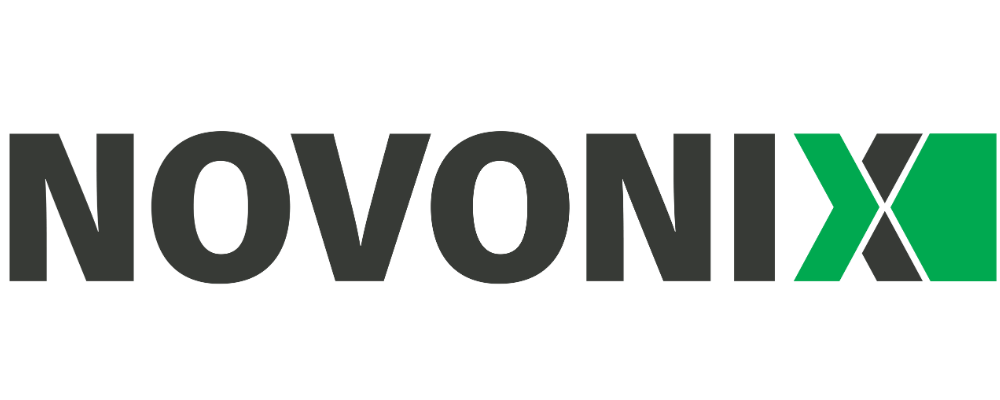
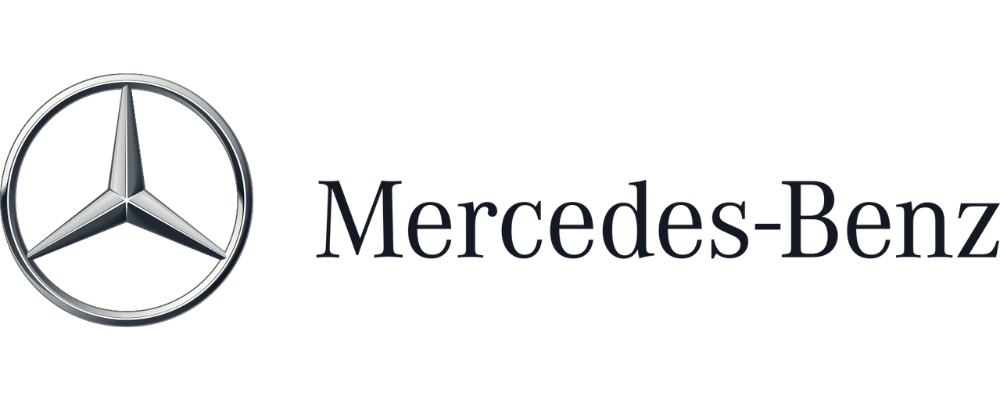
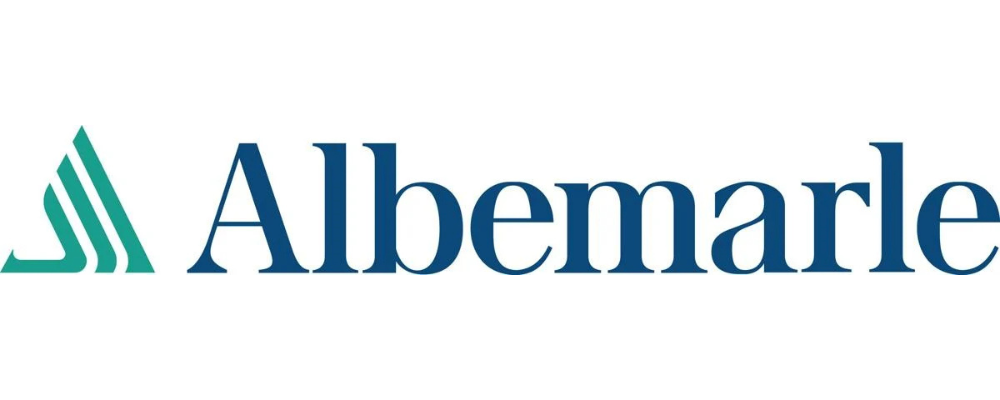
Current defect detection methods are far too
slow—wasting millions as you scale up.
slow—wasting millions as you scale up.
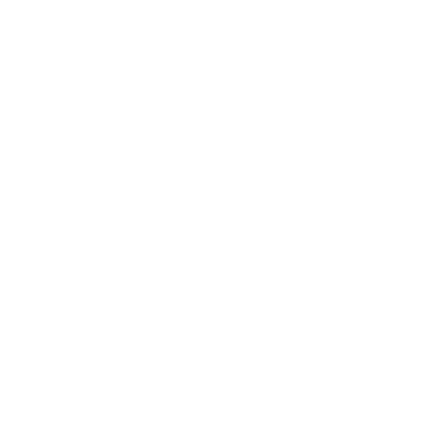
Weeks-long QA misses quality issues.
End-of-line QC takes days or weeks after production to spot defective cells, and often doesn’t catch all problem cells before they are shipped.
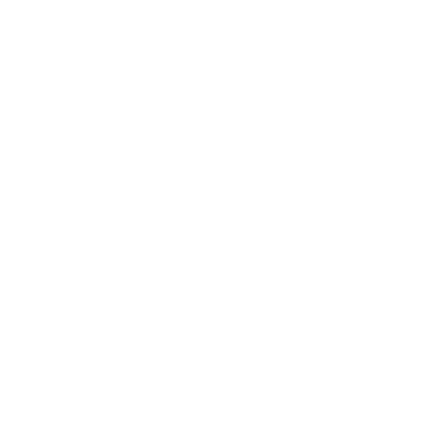
Slow, inefficient root cause analysis.
Pinpointing root cause is a cumbersome process of gathering and plotting many disparate data streams to get the full picture and identify actionable next steps.
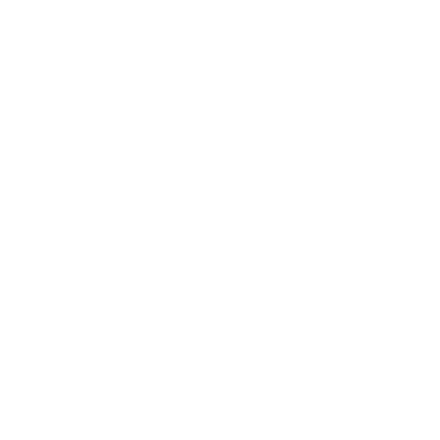
Burning cash on scrap and overhead.
Delays in detecting and resolving quality issues mean weeks of scrapped production, and paying to keep your factory running while you figure it out.
Identify issues faster and decrease your battery scrap rate.
ROOT CAUSE ANALYSIS
Diagnose the cause of manufacturing issues promptly.
In a few clicks, identify which upstream processes and materials led to the defects — giving you the whole picture at once.
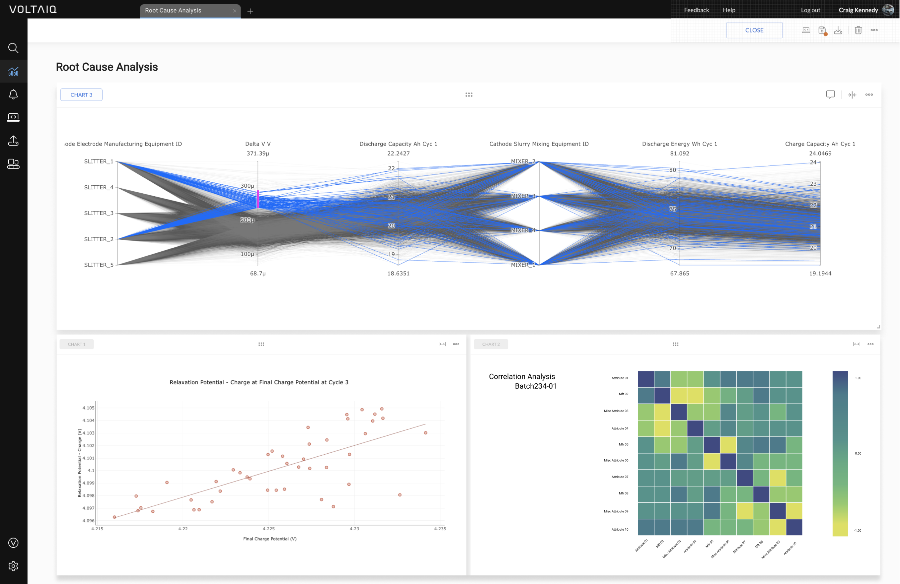
ALERTS
Catch battery quality issues immediately.
Get alerted to problems within the first hours of formation, weeks sooner than existing QA processes, so you can find and fix upstream issues faster.
.png)
NO-CODE ANALYSIS
Plot essential data in seconds compared to days using standard methods.
Run advanced statistical analysis in a matter of clicks including voltage vs. capacity curves, DCIR vs. cycle number, pulse analysis, dQ/dV and much, much more.
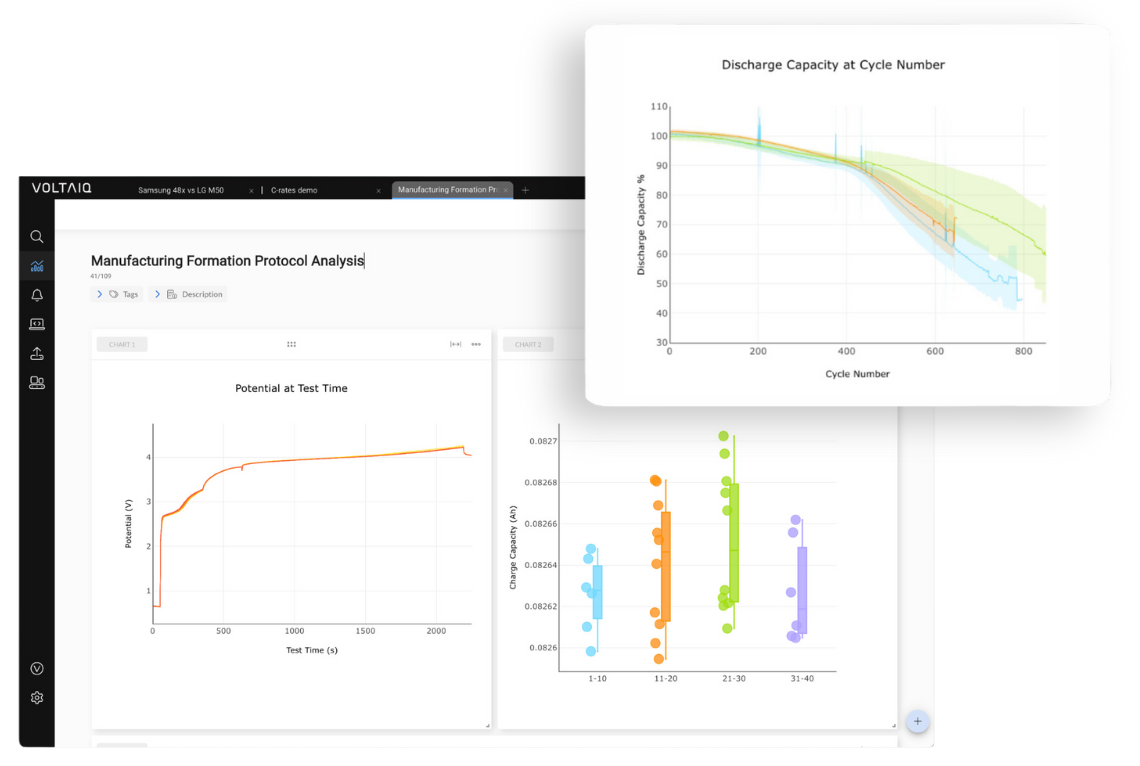
VISUALIZATIONS
Understand the full context of an issue in just a few clicks.
Easily configure and share visualizations that break down defects by frequency, process, or equipment, eliminating tedious manual data collection and processing.
.png)
SHARABLE DASHBOARDS & REPORTS
Easily communicate the issue for faster resolution.
Quickly generate reports and dashboards to share your findings with colleagues, suppliers, partners, customers, and other stakeholders, without any manual data collection and analysis.
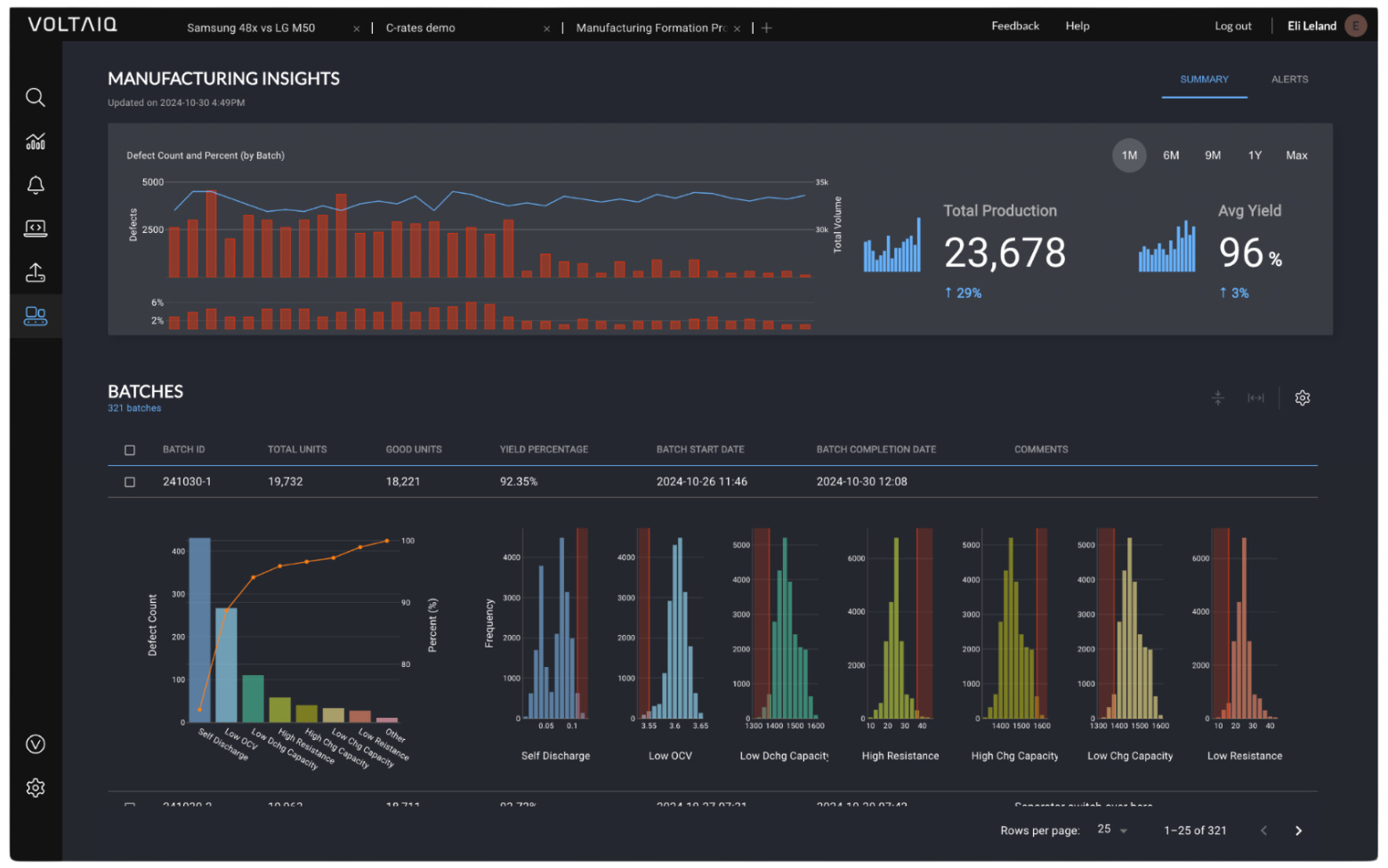
ROOT CAUSE ANALYSIS
Diagnose the cause of manufacturing issues promptly.
In a few clicks, identify which upstream processes and materials led to the defects — giving you the whole picture at once.
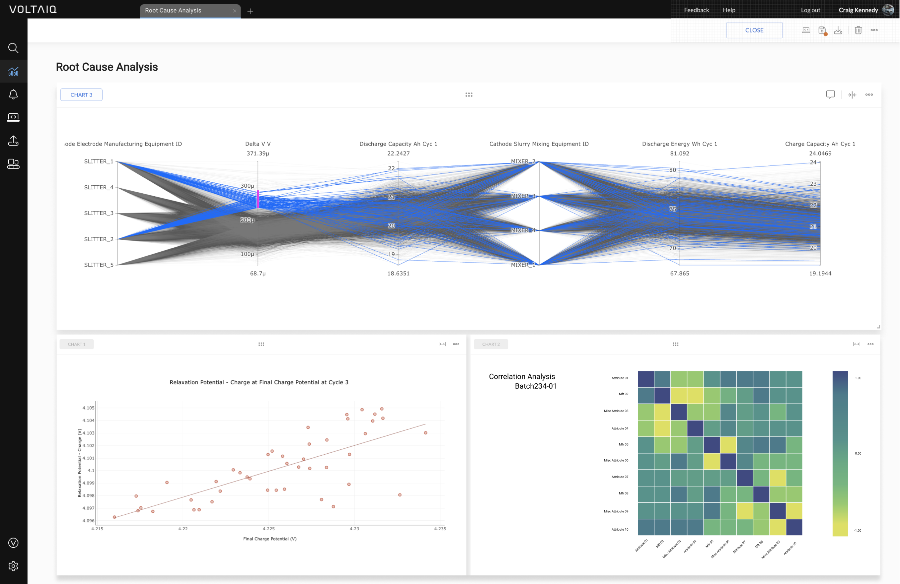
ALERTS
Catch battery quality issues immediately.
Get alerted to problems within the first hours of formation, weeks sooner than existing QA processes, so you can find and fix upstream issues faster.
.png)
NO-CODE ANALYSIS
Plot essential data in seconds compared to days using standard methods.
Run advanced statistical analysis in a matter of clicks including voltage vs. capacity curves, DCIR vs. cycle number, pulse analysis, dQ/dV and much, much more.
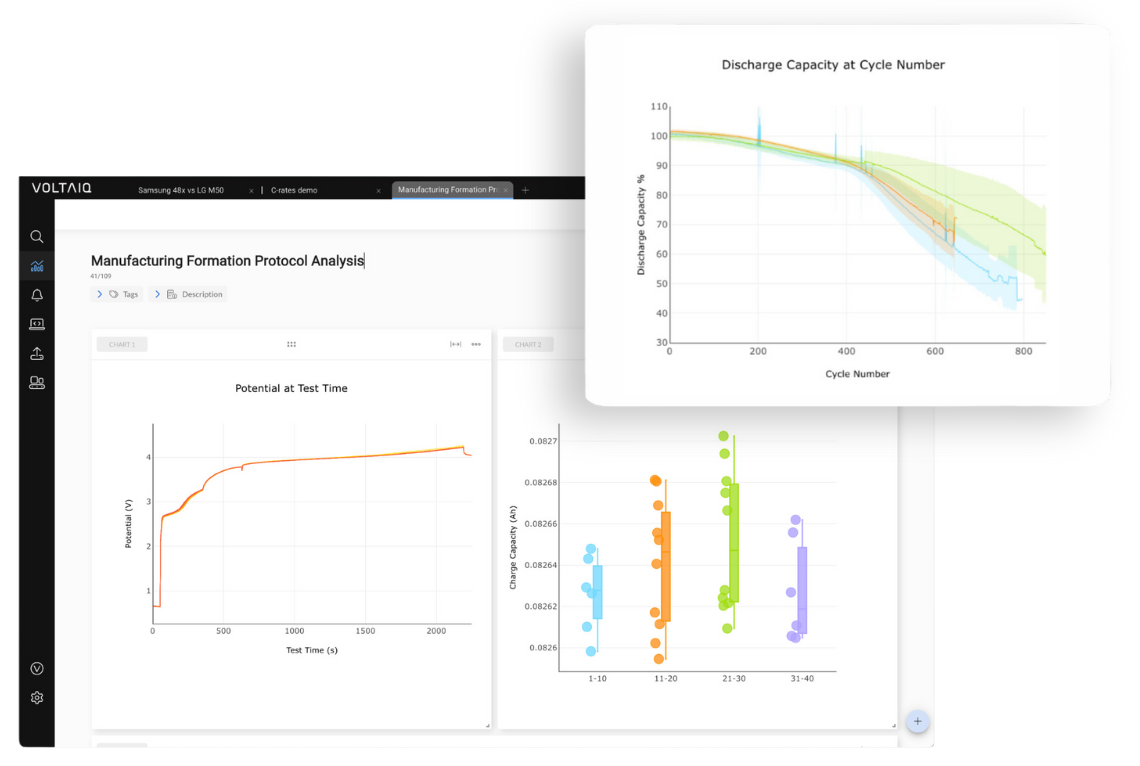
VISUALIZATIONS
Understand the full context of an issue in just a few clicks.
Easily configure and share visualizations that break down defects by frequency, process, or equipment, eliminating tedious manual data collection and processing.
.png)
SHARABLE DASHBOARDS & REPORTS
Easily communicate the issue for faster resolution.
Quickly generate reports and dashboards to share your findings with colleagues, suppliers, partners, customers, and other stakeholders, without any manual data collection and analysis.
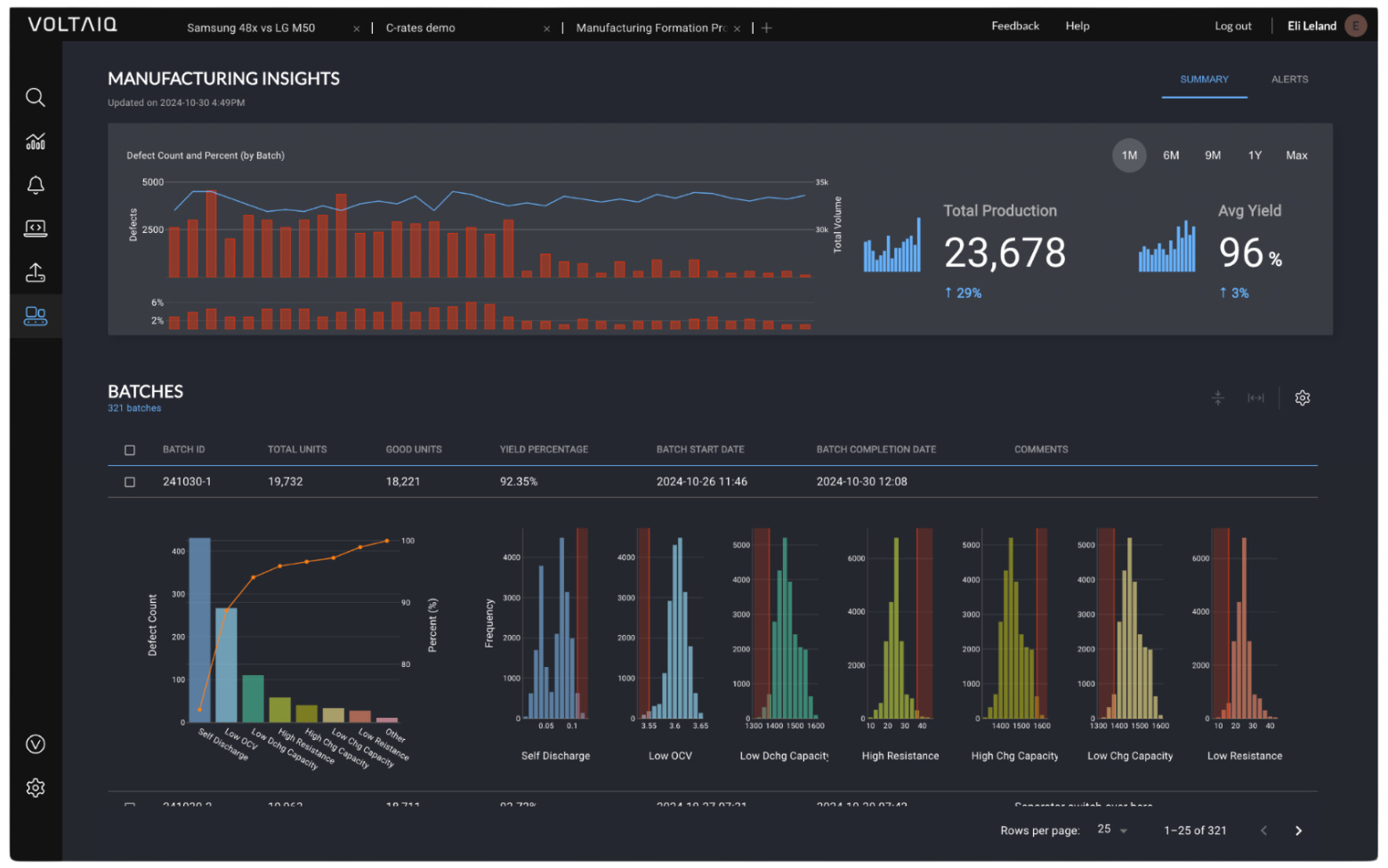
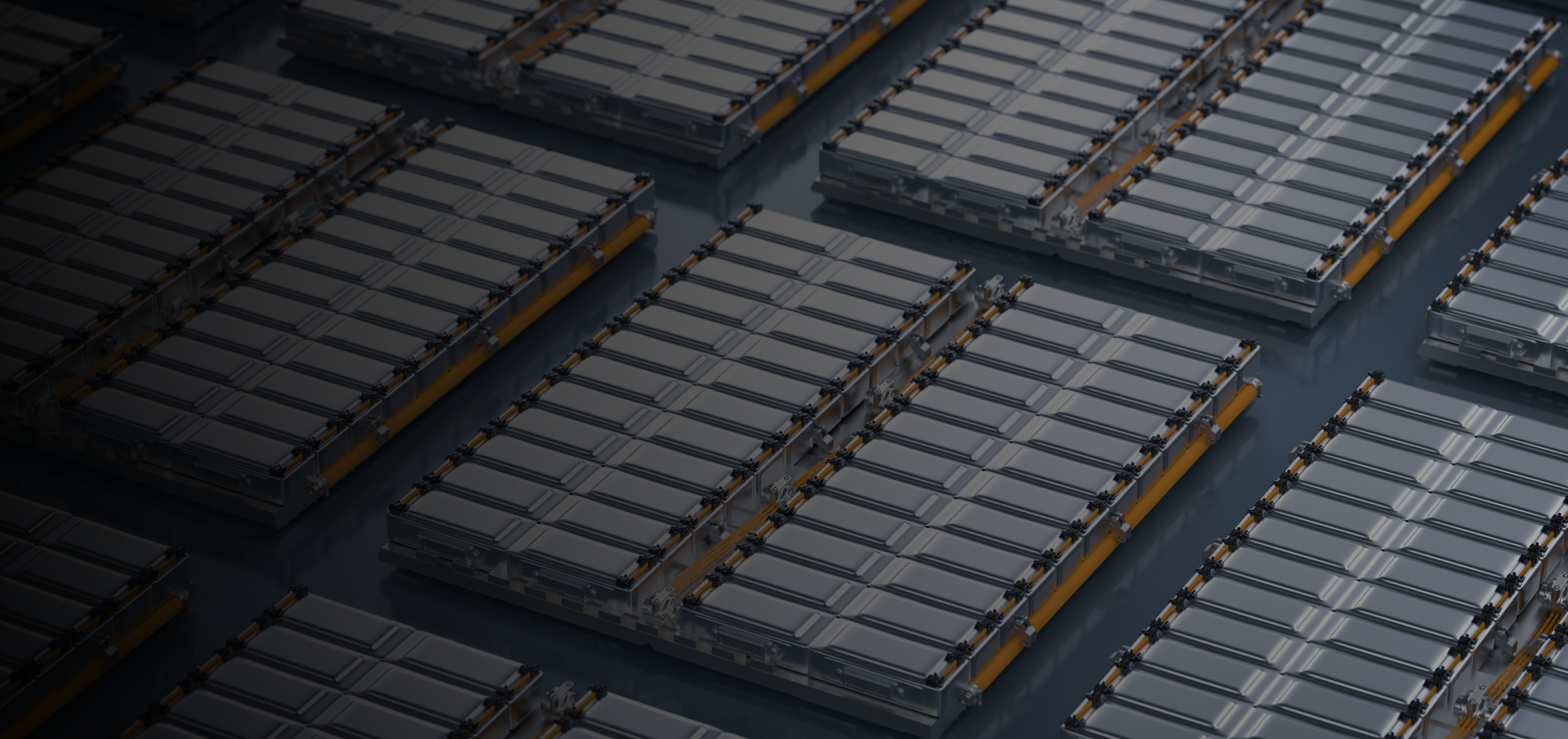
Upskill your engineers
to scale efficiently.
Empower your engineers to better identify root causes of production issues. Tap into Voltaiq's deep bench of electrochemical expertise to scale fast and effectively with training and consulting services, from battery fundamentals to advanced electrochemistry and process development. Available with your Voltaiq subscription in a consultative partnership.
How teams are using Voltaiq:
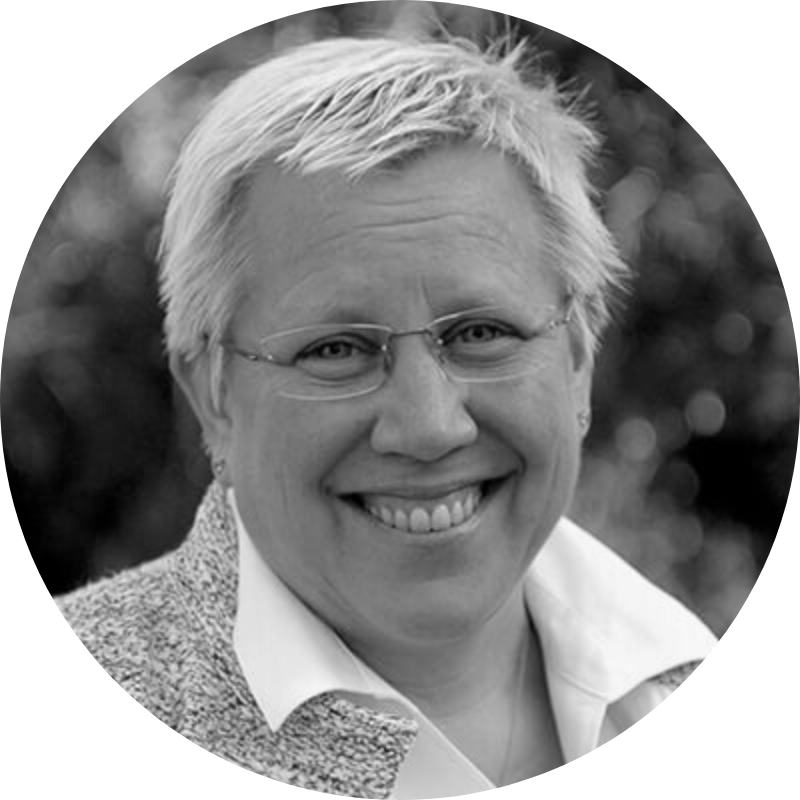
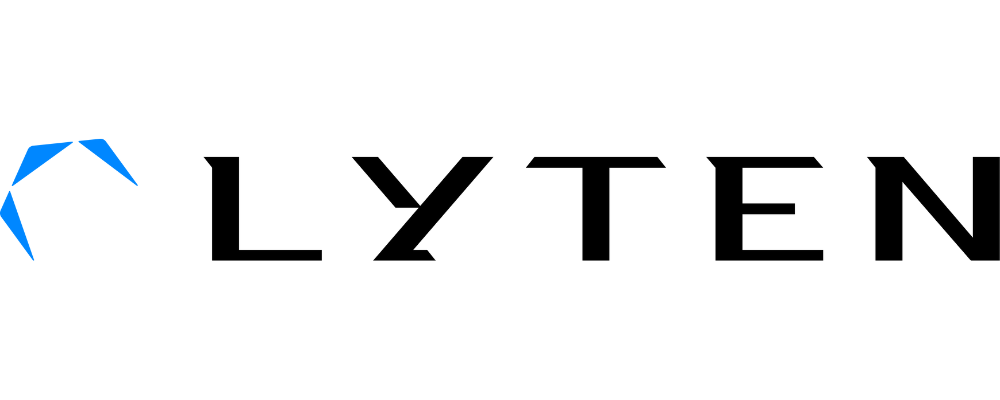
“Voltaiq helps us scale-up and run battery production efficiently, enabling my engineers to quickly pinpoint and resolve issues so we can keep moving forward.”
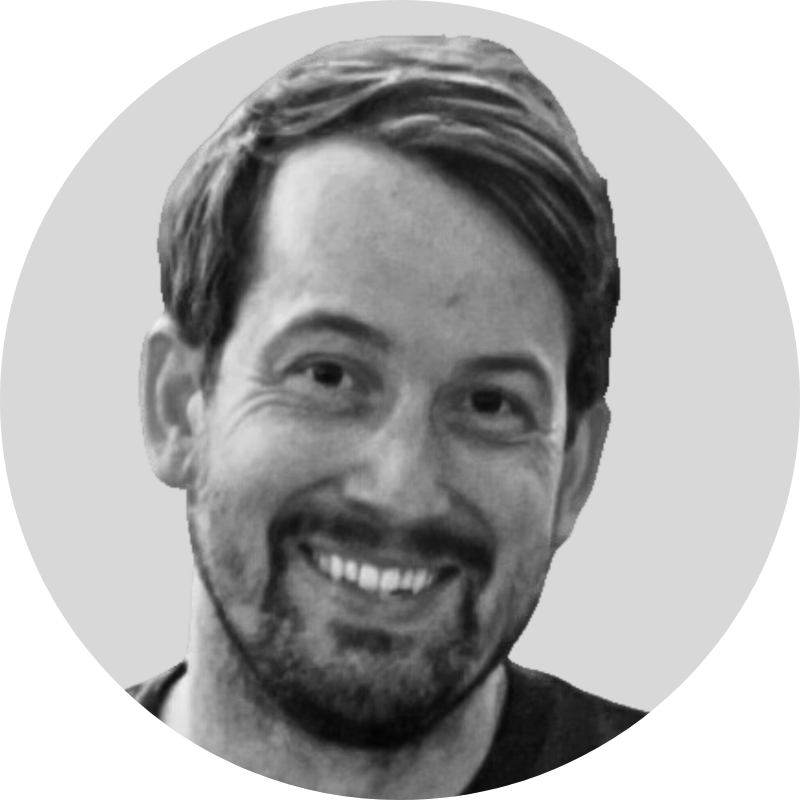
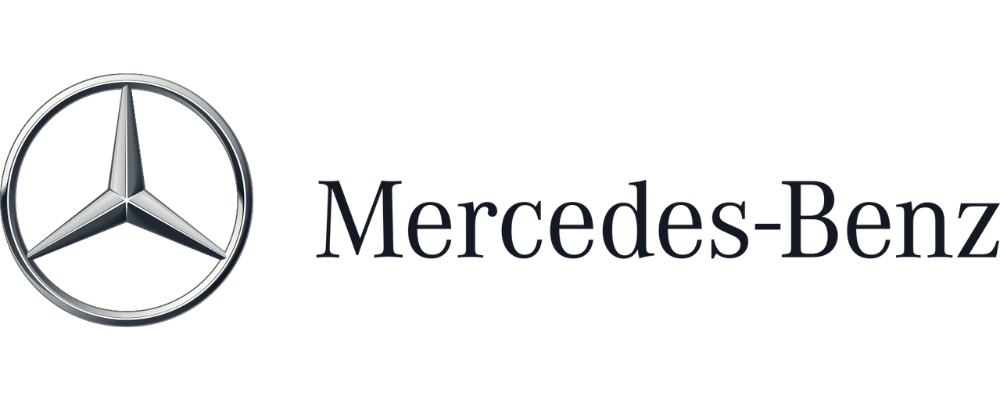
“With Voltaiq, we run a modern distributed battery program at a 70% lower cost. Most importantly my team can focus on battery engineering instead of data wrangling.”
Research & Development North America
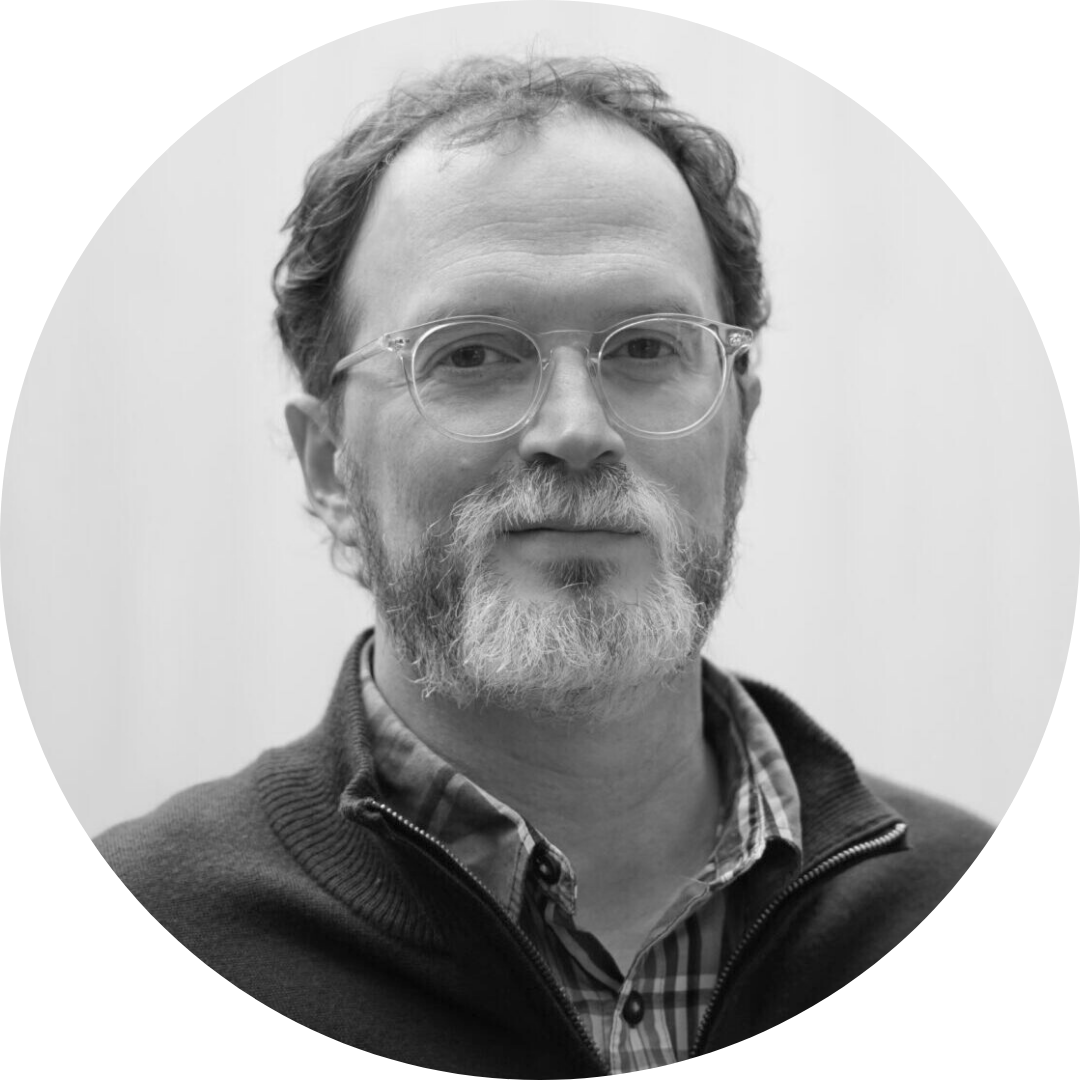
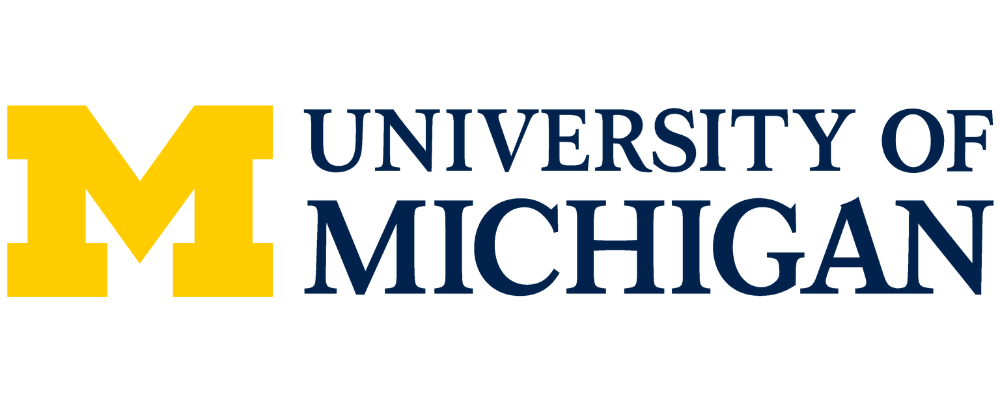
“Voltaiq is such a game-changing solution. Eight years later and we’re still very impressed. I don’t understand why there is any barrier to adopting it. If you’re wondering if you can afford it, you can. You should be doing it. You’ll get more, better organized data with faster access. It’s a no-brainer.”
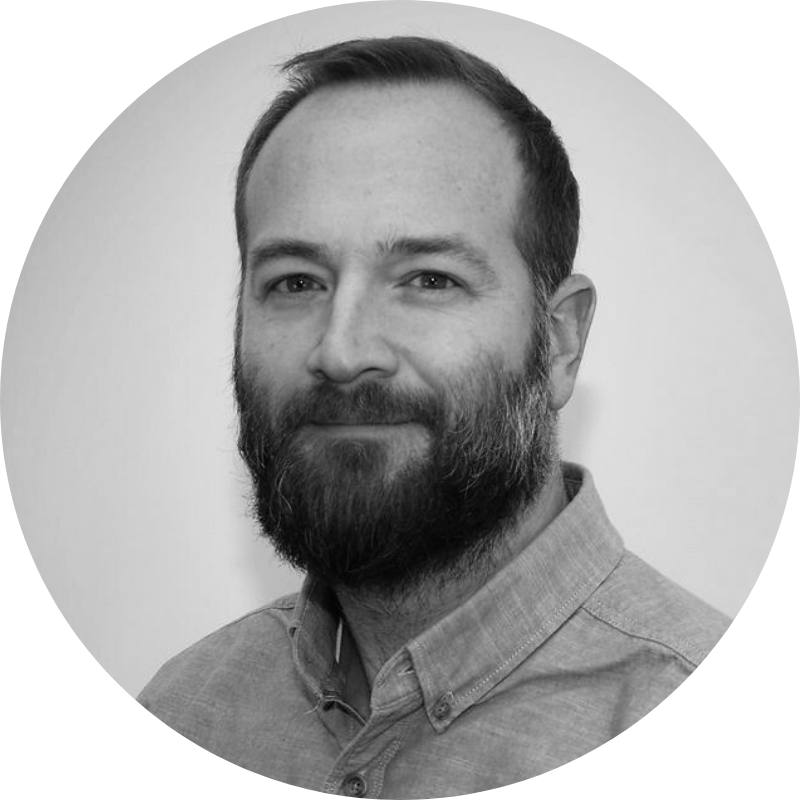
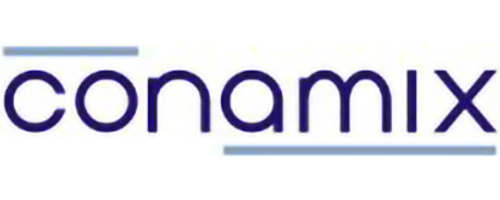
“Everybody uses Voltaiq. We’ve experienced much more rapid product development. We're able to see more of the data, more quickly, in more detail to make better decisions.”
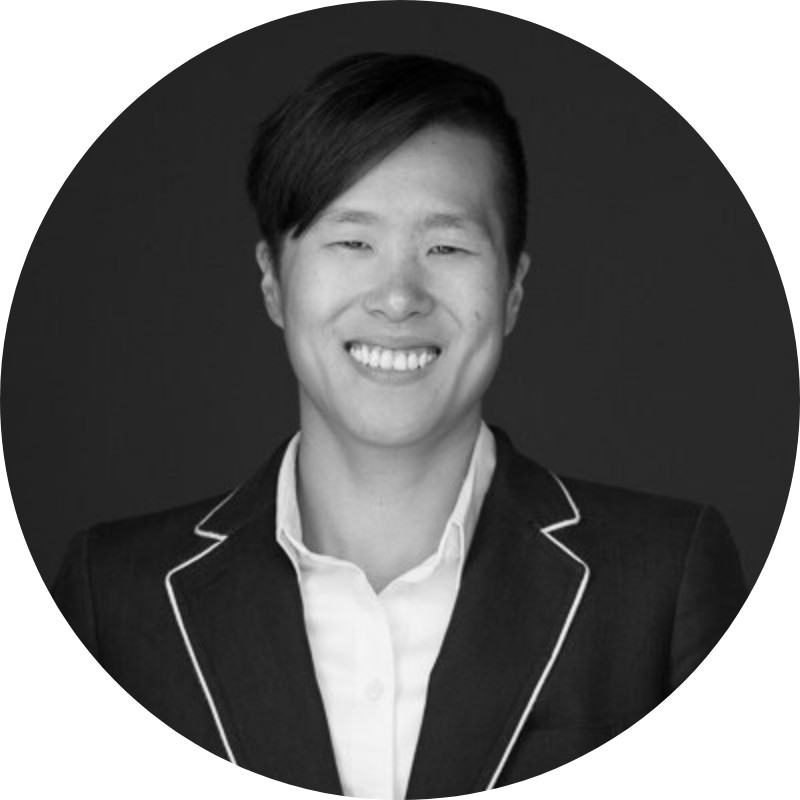
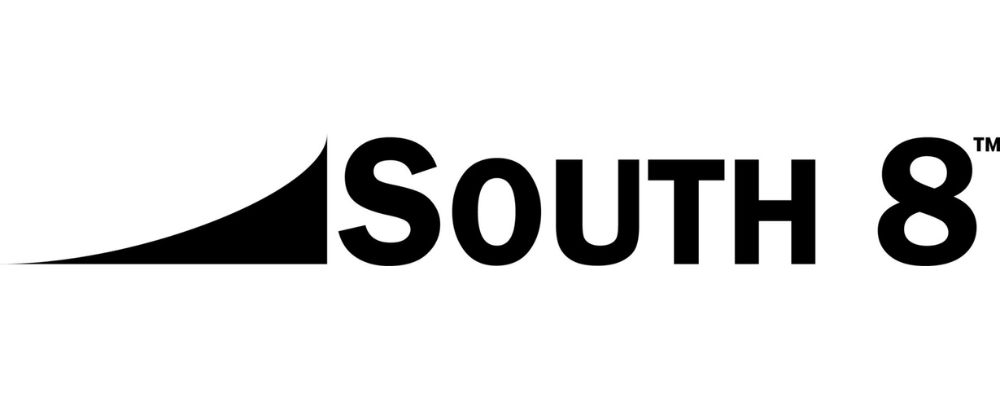
"It’s the time savings. To do root cause analysis, FA, containment, and deployment of solutions. Also faster time for process development. What the ultimate comes down to is yield target and cost target. It all goes hand in hand."